“From the beginning, we have incrementally advanced our use of automation to maintain the highest levels of freshness, accuracy and predictability in our shipments to customers. But at some point, you have to take a big step to ensure you can continue to manage growth and support changes to the business.” Jason Adamchik, Senior Vice President, Automation and Engineering at HelloFresh
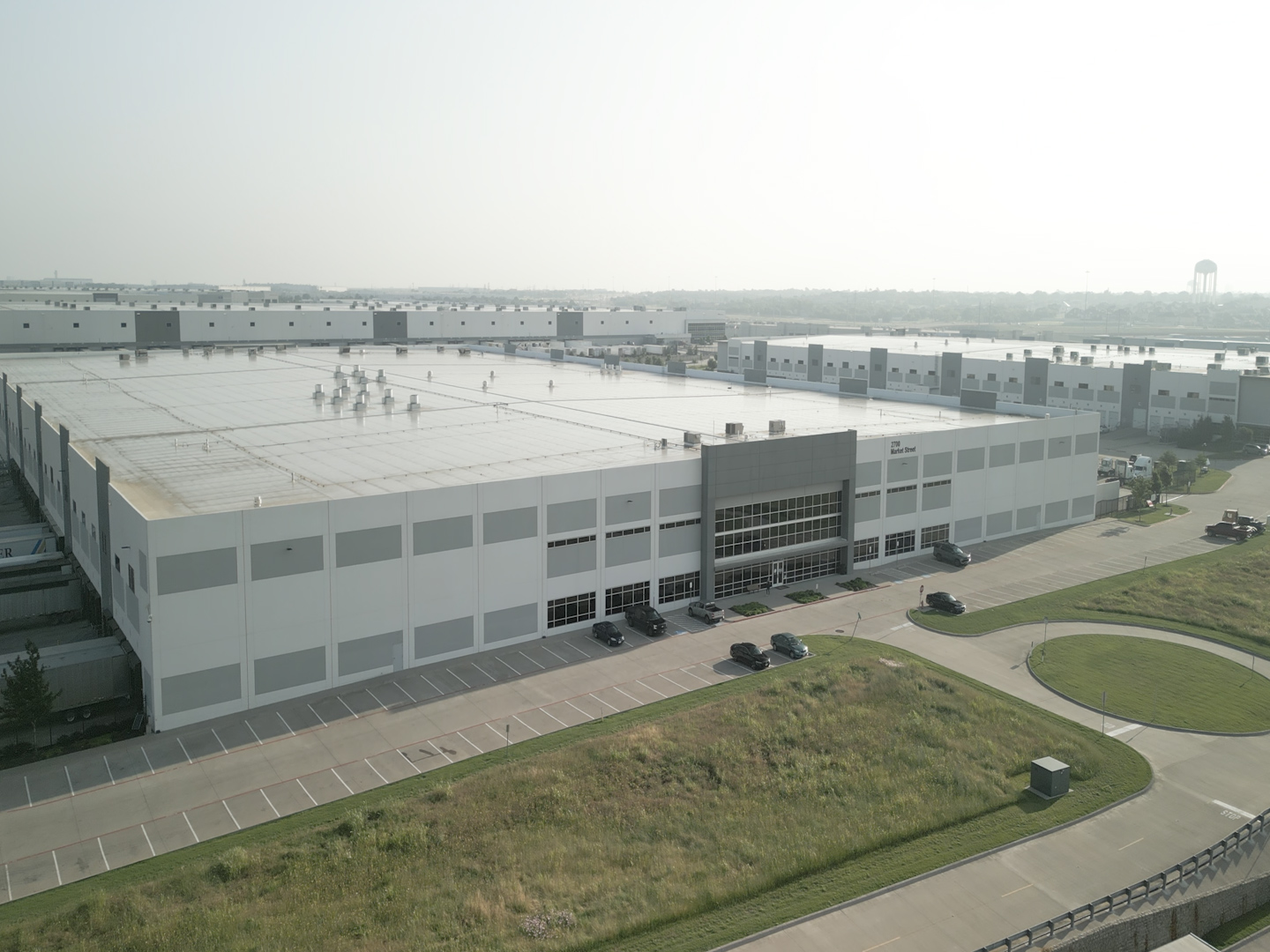
The HelloFresh distribution center in Irving, Texas.
As a leader in meal kit delivery, customers are constantly looking for differentiation and customization in our HelloFresh offerings. With this, our teams found that an enhanced level of automated fulfillment technology would help us manage the different stages of our complex orders.
When we launched our distribution center in Irving, Texas, we had the exciting opportunity to introduce a higher level of automation to our fulfillment lines, which not only added the capacity needed, but also enabled the continued expansion of our inventory.
Read on to see how automation is helping HelloFresh be recognized as an innovator in the food-tech space and ensuring that we provide our customers with a best-in-class experience—and even more flexibility when it comes to meal choice.
The Challenges and Unique Solution
As our HelloFresh customer base has grown over the years, as have our product offerings. Today, our subscribers can customize their meal plans from over 50 weekly recipes and 100+ convenience items. This means that an outbound container can include 16 items, all of which have to be packed in a prescribed order through a process that happens in a chilled environment of 33° F.
“This is a complex process from a fulfillment standpoint that has to be executed with a high degree of precision and speed,” said Kyle DeGroot, Vice President, Operations Engineering & Technology, who was charged with developing the technology plan for the new distribution center.
With Kyle’s guidance, the team formed partnerships with Autostore, a storage and retrieval system that’s operated by autonomous robots, and Swisslog, one of the world’s leading logistics and automation companies.
The vision was to leverage the reliability and speed of AutoStore for the assembly process, with Swisslog helping to establish the new automated distribution center.
However, there weren’t any models within the industry to follow. Together, the teams designed a unique solution including a nearly 30,000-bin AutoStore system featuring 150 robots, 18 carousel ports for picking, 11 conveyor ports for induction to support our high inventory turnover rate, and 4 quality control ports.
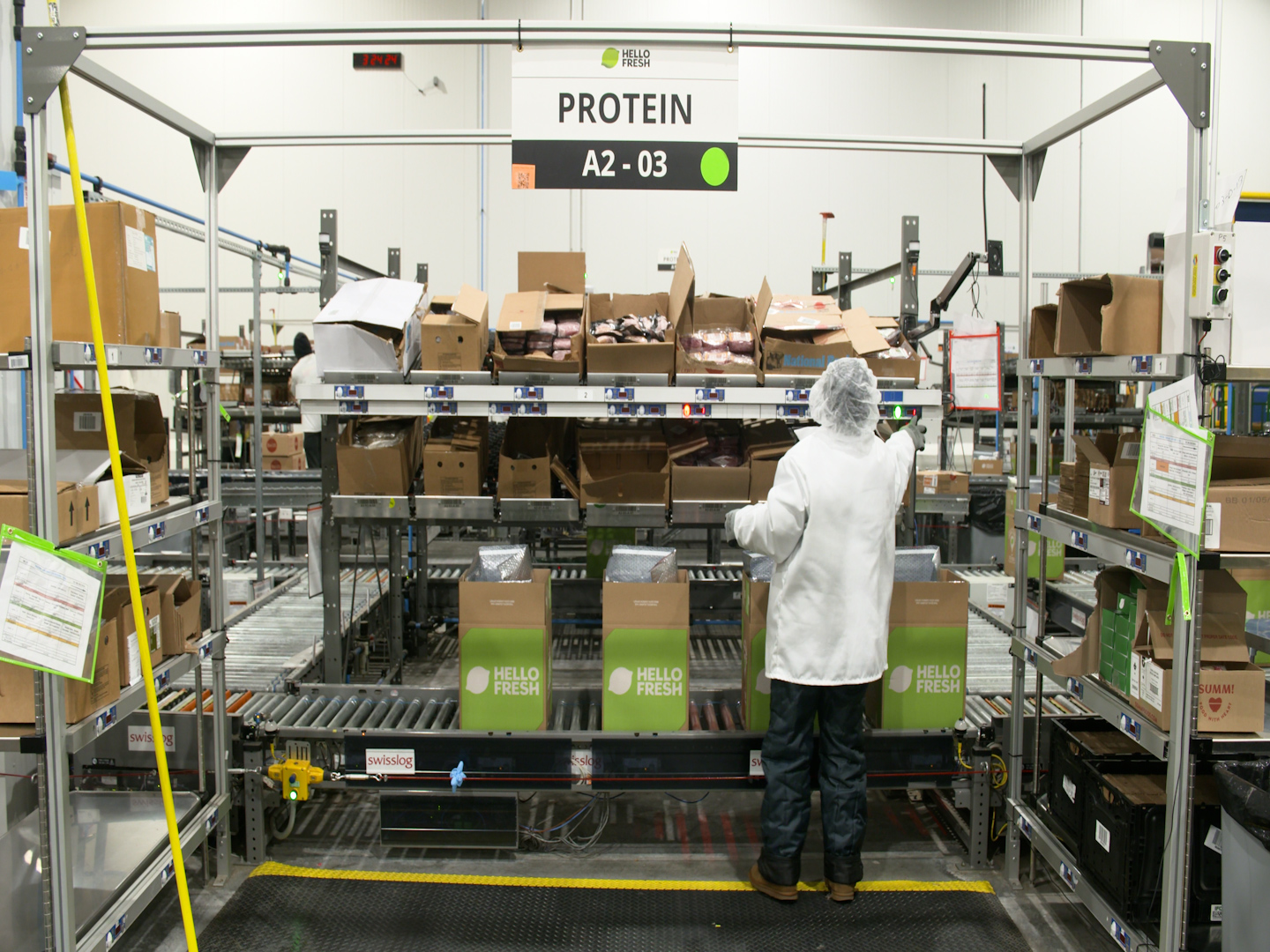
Our automation technology has accelerated production, improved speed, streamlined productivity, and provided better efficiency.
The Benefits of Automation Technology
For HelloFresh, this automation technology has accelerated production, improved speed, streamlined productivity, and provided better efficiency. It helps us to increase capacity levels so we can ship meals to more customers and allows for 500 to 2,000 different add-ons and increased meal choices.
For our employees, simplified computer interactions make the job easier and ensure a safer system. Other benefits include:
- Increased Fulfillment Speed: Automation reduces order cycle times, ensuring freshness as volumes grow.
- Increased Throughput: The high-volume solution helps us to manage growing demand without compromising customer service.
- Enhanced Inventory Management and Visibility: We now have centralized visibility into all inventory, which allows us to manage it based on a first-expired, first-out strategy.
- Improved Productivity and Accuracy: In improving accuracy and increasing productivity, we can continue to add new items without increasing fulfillment complexity.
“The solution gives us the flexibility to easily expand the number of ingredients we support without introducing complexity into our fulfillment processes,” said Jason Adamchik.
As a company that is dedicated to continuously improving—we can’t wait to see how our future automation efforts continue to enhance our customer experience.